The Past, the Present and the Future of High Temperature Corrosion Research - an EFC View
M. Schütze
1. Introduction
For the average person high temperature corrosion is an unknown factor in daily life since the consequences of high temperature corrosion are usually not obvious. The reason is that high temperature corrosion occurs behind walls as high temperature processes are usually shielded from their environment. However, this type of corrosion can be life-time and performance-determining in a number of everyday examples, for instance automotive engines (exhaust parts, catalyst carriers), jet engines, household heating systems, energy conversion systems (fossil power stations), petrochemical and chemical process industries. Most of these applications became of technical importance at the end of the nineteenth and the beginning of the twentieth century, which is the reason why (as will be shown later) high temperature corrosion only started to appear in the literature at that time. It was in particular in the second half of the twentieth century when high temperature corrosion research became a major key to increasing efficiency and reliability in the industrial areas mentioned above and due to ambitious requirements in high temperature operation following demands for even higher efficiencies and lower emissions of environmentally hazardous compounds research in this field is still characterized by a dynamic development.
In the European Federation of Corrosion (EFC) the topic high temperature corrosion has been part of its work for about 40 years. As the EFC celebrated its 50th anniversary in 2005 this was an opportunity to look back on the history of high temperature corrosion and on its role in the activities of the Federation. Furthermore this was an occasion to reflect on the present developments in the field and where possible on those of the near future. The aim of this paper is to underline the role of high temperature corrosion research for established and advanced technologies and also to provide an eye-opener as to how much basic understanding had already been achieved in the very first years of research in this field.
2. History
As a common approach today to find out about the history of a technological development an Internet search can be very useful. If one uses this approach for high temperature corrosion the results can be rather frustrating and it is actually only if one searches by the keyword ‘corrosion’ that some more or less satisfactory information can be found. This situation is also very much illustrated by the ‘timeline of corrosion history’ /1/, which is given in Table 2.1.
Date |
Landmark |
Source |
412 BC |
Antifouling paint |
Unknown |
1675 |
Mechanical origin of corrosiveness and ‘corrodibility’ |
Boyle |
1763 |
‘Bimetallic corrosion’ |
HMS Alarm report |
1788 |
Water becomes alkaline during corrosion of iron |
Austin |
1791 |
Copper-iron electrolytic galvanic coupling |
Galvani |
1819 |
Insight into electrochemical nature of corrosion |
Thenard |
1824 |
Cathodic protection of Cu by Zn or Fe |
Sir Humphrey Davy |
1830 |
Microstructural aspect of corrosion (Zn) |
De la Rive |
1834-40 |
Relations between chemical action and generation of electric currents |
Faraday |
1836 |
Passivity of iron |
Faraday, Schoenbein |
1904 |
Hydrogen overvoltage as a function of current |
Tafel |
1905 |
Carbonic and other acids are not essential for the corrosion of iron |
Dunstan, Jowett, Goulding Tilden |
1907 |
Oxygen action as cathodic stimulator |
Walker, Cederholm |
1908-10 |
Compilation of corrosion rates in different media |
Heyn, Bauer |
1910 |
Inhibitive paint |
Cushman, Gardner |
1913 |
Study of high temperature oxidation kinetics of tungsten |
Langmuir |
1916 |
Differential aeration currents |
Aston |
1920-3 |
‘Season-cracking’ of brass = intergranular corrosion |
Moore, Beckinsale |
1923 |
High temperature formation of oxides |
Pilling, Bedworth |
1924 |
Galvanic corrosion |
Whitman, Russell |
1930-31 |
Subscaling or ‘internal corrosion’ |
Smith |
1933 |
Probabilistic nature of corrosion |
Evans |
1931-9 |
Quantitative and electrochemical nature of corrosion |
Evans |
1938 |
Anodic and cathodic inhibitors |
Chyzewski, Evans |
1938 |
E-pH thermodynamic diagrams |
Pourbaix |
1950 |
Self-accelerating (autocatalytic) nature of localized corrosion |
Uhlig |
1956 |
Tafel extrapolation for measurement of kinetic parameters |
Stern, Geary |
1968 |
Electrochemical noise signature of corrosion |
Iverson |
1970 |
Electrochemical impedance spectroscopy (EIS) |
Epelboln |
Table 2.1: Timeline of corrosion history /1/
This table presents some historical landmarks of discoveries related to the understanding and management of corrosion.
While the first citation, dealing with protection against aqueous corrosion (a type of corrosion which, of course, is much more obvious in daily life), dates back to 412 BC, the first reference to high temperature corrosion in this list is found for the year 1913. A more detailed search outside this historical compilation in Table 2.1 reveals that high temperature corrosion already played a role in much earlier times and one nice example is the Chimú culture in South America which had its heyday between 1250 and 1460 AD /2, 3/. In this culture the Tumbago technique was developed which used Au-Cu alloys (with Cu up to 70%) as a material which had the appearance of gold but avoided several of its drawbacks. These alloys had a lower melting point, but a higher strength than gold. By heating these alloys in a simple furnace selective oxidation of Cu took place on the surface, while the sub-surface became strongly enriched in Au. The process of selective oxidation combined with enrichment/depletion processes in the sub-surface zone is actually the key to the life-time and performance of all today’s technical alloys and it was modelled in the first half of the twentieth century (see later). The Tumbago technique, however, served for the production of a surface of pure gold on the less costly Au-Cu alloys when the copper oxide had been removed by rapid cooling (spalling of the oxide due to differences in the coefficients of thermal expansion of metal and oxide, an issue which again is of the highest importance for technical materials today) or by vegetal acid. Thus the Chimú culture already used fundamental aspects of high temperature corrosion for manufacturing components with optimized bulk and surface properties several hundred years ago, an approach which sounds quite familiar to those aiming at the development of processes for functional surfaces on alloys today.
In recent years metal dusting as a corrosion mechanism has become of increasing interest in research, see e.g. ref. /4/. However, the first report on coke deposition in a technical process as the mechanism which may end up in metal dusting dates back to 1876 /5/. This paper describes in detail the situation in which ‘carbonic oxide in the gas is decomposed with the ultimate formation of carbonic acid and solid carbon’.
The most spectacular example of high temperature corrosion in the early days of chemical process industries, however, dates back to the beginning of the 20th century. In those days the process of industrial ammonia production was developed and for this process large amounts of high-pressure hydrogen had to be converted at higher temperatures in the ammonia reactor. In extreme cases these reactors, which were made from carbon steel, had life-times of only little more than three days until they fractured due to dissolution of the strengthening carbides in the steel by the formation of methane from the carbides and hydrogen /6/. What remained was a porous spongy iron material without any mechanical strength. While today this type of high temperature corrosion is suppressed by alloying the steels with strong carbide formers, e.g. Cr and Mo, in the old days the double wall tube was used which consisted of an inner quasi carbon-free mild steel tube which was not prone to hydrogen high temperature attack and an outer load-bearing high strength carbon steel /6/. The latter, however, had been made pervious to hydrogen by a huge number of small holes so that hydrogen that had diffused through the inner mild steel tube wall could escape into the environment without building up critical pressures which are needed for this type of high temperature corrosion.
The scientific discussion of the topic high temperature corrosion started in 1913 with a paper by Langmuir who described the oxidation process of tungsten at low pressures /7/. He observed that oxidation of a metal can lead to a solid scale or a volatile species: ‘A tungsten wire heated in oxygen at low pressure begins to oxidize at about 800 K, the oxide forming a brown or blue coating on the metal. By heating to about 1200 K the oxide volatilises without dissociation and leaves the wire clean and bright.’ He also mentioned that electric charges have to be involved in the oxidation process (‘the oxygen molecule, after taking up a negative charge, is held by electrostatic forces to the positively charged tungsten atoms and soon, by secondary reactions, combines with the tungsten and with oxygen atoms to form WO3’), but admits that ‘the present experiments do not throw much light on the nature of these secondary reactions’.
The parabolic rate law of oxidation, which can be found in all textbooks on high temperature corrosion, was first described by Tammann in 1920 /8/. In the somewhat exotic system silver/iodine vapour of his paper the tarnishing layers on the metal grow according to the well-known rate law:
dy/dt = p/y
or
y˛ = 2pt
where he uses y for the layer thickness and p as the constant which has a strong relation to the diffusion coefficient D of iodine in AgI. The iodine concentration gradient was described by him as
2p = aD dx/dt
where a is a correction factor. The results of his measurements are given in Fig. 2.1 which underlines the parabolic dependence of layer thickness on reaction time.
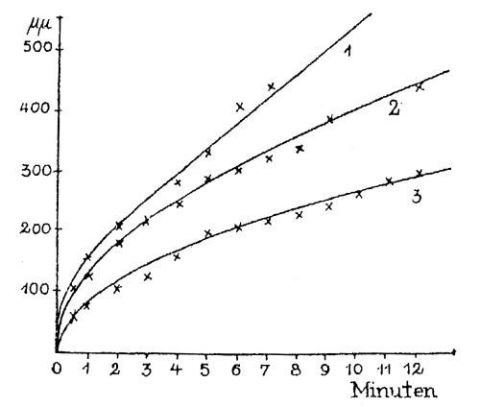
Fig. 2.1: Kinetics of the growth of the tarnish layer on silver in iodine vapour, as observed by Tammann /8/.
The first detailed scientific investigations of the oxidation of several metals in atmospheric oxygen were performed by Pilling and Bedworth /9/ in 1923. They oxidized Cu, Ni, Fe, Zn, Pb, Cd, Ca and Mg with the emphasis on the first three metals and also confirmed the parabolic rate law for the reaction between oxygen and metal and for a number of oxidation times. Some of the sentences in their publication could be from a textbook of today:
‘... the transmission of oxygen through a compact oxide layer is accomplished (a) by the physical solution of oxygen in the solid oxide, (b) the diffusion of this dissolved oxygen from the exterior to the interior surface. The shape of the oxidation curve of the metal with a restraining oxide envelope can be derived without difficulty for a given concentration difference and ... the rate of diffusion is inversely proportional to the length of the path of diffusion, in this case the thickness of the oxide layer. This is a parabolic curve, with the quantity of oxygen combining proportional to the square root of the time of oxidation. The above analysis refers, of course, to physically perfect oxide jackets ...’.
Figs. 2.2 and 2.3 look rather familiar when having read one of the common textbooks
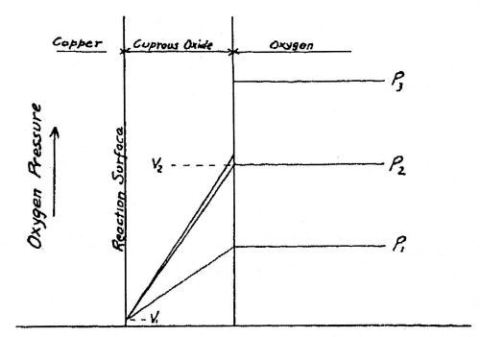
Fig. 2.2: Oxygen partial pressure situation in a growing oxide/metal system, as described in ref. 9.
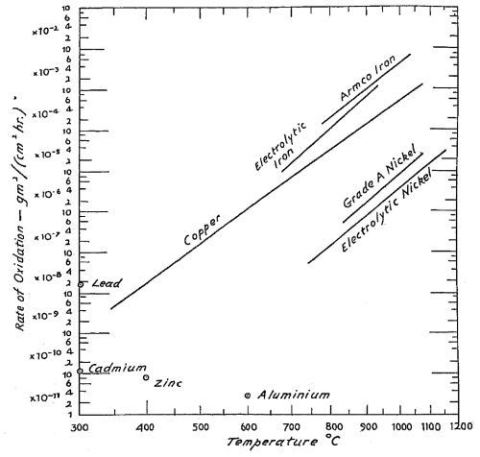
Fig. 2.3: Comparative oxidation rates of several metals (taken from ref. 9)
as, for instance, that of Kofstad /10/. The most well-known results of this paper, however, are those listed in Table 2.2 which describe the volume change taking place when metal is converted into metal oxide.
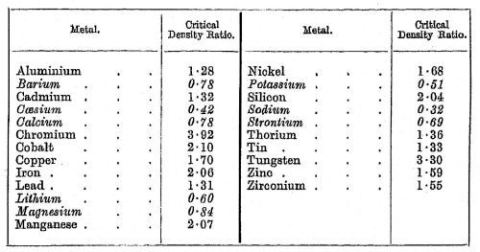
Table 2.2: The Pilling-Bedworth ratios in the original publication
These values are commonly called the Pilling-Bedworth ratio. As a conclusion from this table they distinguish between ‘cellular or discontinuous-type oxides’ where the ratio is less than 1, and ‘compact or continuous-type oxides’ where the ratio is greater than 1. As a general statement they concluded that ‘... the group of metals forming cellular oxides comprises the majority of the so-called light metals; that of all of the heavy metals fall into the group of conpact coatings’. The latter type of oxides was regarded as protective and even today many of their findings are still being used to explain the stress situation in oxide/metal systems /11/ although some of these considerations can be misleading /12/.
In 1926 Dunn analysed the work of Pilling and Bedworth in detail and based on his own experimental work came to the conclusion that the parabolic law applies only to ‘an oxide film whose properties remain constant in time’ /13/. He furthermore realised the necessity ‘to formulate a more fundamental theory of oxidation and diffusion’. In his paper he outlined a theory of diffusion in solid solutions and deduced an expression for the variation of diffusion rate with temperature based on the application of established laws to the thermal agitation of solids. The origin of a departure from the ideal parabolic law has been traced by him to changes appearing in the oxide film during oxidation /14/.
The Pilling-Bedworth work also stimulated investigations in Japan by Utida and Saito /15/. They oxidized a number of heating wires (Nichrome, Chromel, etc) and found out that after initial rapid oxidation the rates may slow down dramatically once a protective oxide scale has formed. The oxidation rates furthermore depended on the amount of Fe in the alloy. The fact that after an initial rapid oxidation a much slower growth rate in a period of protection follows is typical of most of today’s technical high temperature alloys.
A significant part of the fundamentals of iron and steel oxidation was laid by Pfeil in 1929 /16/. He describes the appearance of three different oxide layers differing in structure and composition. ‘With a few exceptions non-ferrous elements present in the iron before the oxidation are concentrated in the innermost of the three layers’. The mechanism of oxidation consists of ‘counter-current diffusion - the iron diffusing outwards and the oxygen inwards through the scale ...’. This was concluded from the fact that ‘foreign substances placed on the surface of the iron are not forced away by the formation of the scale, but remained unmoved and became completely enveloped by the scale’. Pfeil has, however, also become well-known (possibly even better known) by his patent in 1935 which laid the grounds for the reactive element effect /17/. This patent describes how ‘increased life is imparted by adding to the alloy one or more of the rare earth metals ... in such a quantity that if there is any residue in the finished alloy it does not exceed 0.5%’.
Starting in 1933 a number of very significant contributions to the theory of oxidation of metals in alloys were published by Wagner which still form the most comprehensive theoretical basis even in today’s discussion of the mechanisms of high temperature corrosion. Three key papers shall be mentioned here /18-20/. The first of these papers establishes the diffusion theory of the oxide scales, the second analyses the situation of oxide scale nucleation and growth on binary alloys and the third discusses the role of alloy composition and sub-surface zone depletion on the course of oxidation of alloys in a quantitative manner. The last paper was also the first in which the transition between internal oxidation and the formation of a continuous oxide layer has been modelled.
There have been quite a number of other pioneering papers in the field which, can, however, not be quoted here due to space limitations. Only two more (perhaps arbitrarily chosen papers) shall be briefly mentioned. In 1979 the importance of the role of mechanical aspects in high temperature corrosion was pointed out very clearly in an overview paper /21/ which stimulated a number of research projects in this field, part of which have been summarized in /12/. The other one, which appeared in 1980, represents an excellent summary of the reactive element effect /22/ which is one of the most important issues for increasing the resistance of technical alloys to oxidation at high temperatures.
3. High temperature corrosion in the European Federation of Corrosion
The need to treat high temperature corrosion issues as part of the EFC activities was identified in the early sixties of the last century. At their meeting on 27 April 1965 the Board of Administrators initiated a foundation committee for a working party on high temperature corrosion. On 11 November 1965 the foundation committee met in Frankfurt am Main and prepared a request to the national member societies to nominate candidates for a new working party by 1 March 1966. Evidently things went quite slowly and a reminder had to be sent out on 9 August 1967. This reminder had the effect that nomination letters could be sent out to the members of the new working party a little later and the first official meeting took place on 17 October 1967 in Düsseldorf. The new working party was named ‘Corrosion by Hot Gases and Combustion Products’, received the number ‘EFC Working Party 3’, and was chaired by Alfred Rahmel until July 1986. The first members of this working party are listed in Table 3.1. The first task of the working party was to draft a questionnaire in order to find out topics of interest among the member societies in this area.
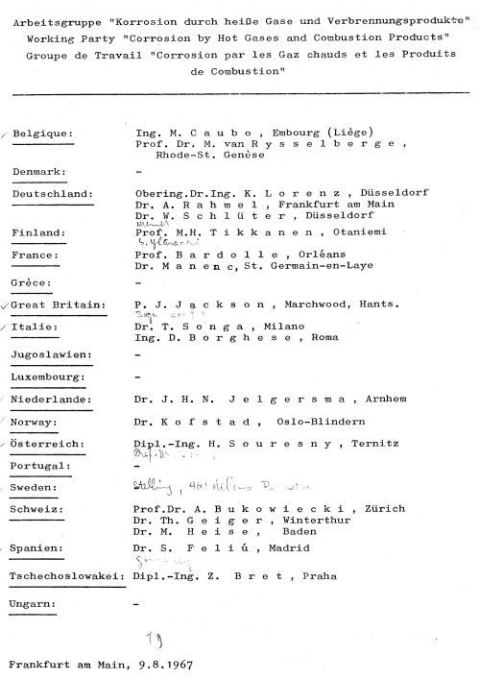
Table 3.1: The first members of Working Party 3 after its foundation in 1967
The questionnaire contained 18 topics from fundamental and applied research as well as from industrial application. The evaluation of the replies was finished on 21 August 1969 and as a result a workshop on the role of trace elements in metals and alloys for the protection of steels was organized on 9-10 December 1970 in Düsseldorf. About one year earlier a workshop on corrosion in molten salts had already taken place in Düsseldorf on 10-11 April 1969 under the auspices of the newly formed working party. Until December 1970 the member society in charge of Working Party 3 was the German Society of Iron and Steel-Makers (VDEh). In the framework of a re-organization the responsibility for Working Party 3 was moved to DECHEMA, Frankfurt am Main. On 3 July 1986 Hans Grabke was appointed as the new chairman of the working party and Michael Schütze joined him as the secretary. Hans Grabke led this working party with great success until 1998. He organized a number of well recognized workshops and sessions with EUROCORRs. After Hans Grabke’s retirement Michael Schütze was elected as the new chairman at EUROCORR 1998 in Utrecht. He continued the tradition and now Working Party 3 organises internationally recognized workshops on high temperature corrosion every two years in Frankfurt and contributes a session to EUROCORR every year. The papers from these workshops and EUROCORR sessions have been published in the journals ‘Materials and Corrosion’ and ‘Corrosion Engineering Science and Technology’ as well as in the form of books in the green EFC series /23-27/.
Since there has always been a lack of test standards despite the industrial importance of the field Working Party 3 has taken over a leading role in the development of ISO guidelines. The first step as a follow-up of an EFC workshop on cyclic oxidation testing /24/ was to initiate a European research project on the development of guidelines for cyclic oxidation testing in 2001. This project included 23 partners from industry and academia based in 11 European countries. The work ended in January 2005 and the draft guidelines developed were submitted to ISO as a work item. In the meantime five work items are on the list of the Work Group 13 ‘High Temperature Corrosion’ of ISO Technical Committee 156 ‘Corrosion of Metals and Alloys’, see Table 3.2, where the convenor is the chairman of Working Party 3 and several members of this EFC working party are also members of the ISO TC 156 WG 13.
Work Item |
Status |
Continuous and discontinuous isothermal oxidation testing |
Voting on CD a) |
General guidelines for post-exposure examination |
Voting on NWIP b) |
Thermal cyclic oxidation testing |
Voting on NWIP b) |
Method of electrochemical corrosion test for metallic materials in molten salts |
Submitted as NWIP b) |
Method of dipping and embedding test in molten salt for metallic materials |
Submitted as NWIP b) |
a) CD: Committee draft, b) NWIP: New work item proposal (status February 2006)
Table 3.2: Work items of Work Group 13 ‘High Temperature Corrosion’ of ISO Technical Committee 156 ‘Corrosion of Metals and Alloys’
One of the major tasks of Working Party 3 will, therefore, in future also be to take care of proper standardization activities in high temperature corrosion in collaboration with the colleagues outside Europe. Another main task of the working party will be the collection and dissemination of knowledge in the form of workshops and publications.
4. The situation of high temperature corrosion research today
In the established technologies high temperature corrosion no longer seems to be a significant hazard as long as the existing knowledge is applied properly. Nevertheless damage cases are observed from time to time due to unexpected operation conditions or improper selection of materials. In the meantime a number of new high temperature processes have been developed or the operation conditions have shifted to more critical situations due to changes in the operation environments or temperatures mainly as a consequence of demands for higher efficiencies, the exploitation of energy-containing waste or critical fuels and a decrease in polluting exhaust gases. Fig. 4.1 summarizes in a simple schematic the temperature ranges and the extent of corrosion for several corrosive species in industrial applications.
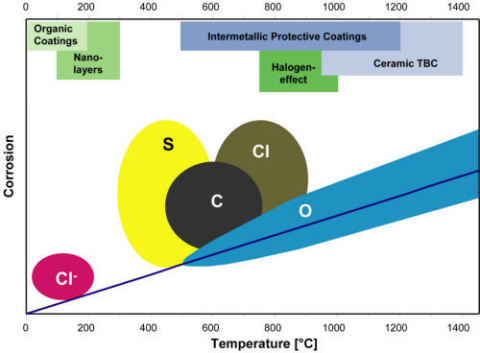
Fig. 4.1: Corrosive species, temperature ranges and extent of corrosion from these species in high temperature operation environments
This figure furthermore contains the protection strategies at the different temperatures which nowadays dominate in high temperature corrosion research, while the investigation of the corrosion mechanisms has taken over rather a secondary role. Since most of the technical alloys, however, have come close to an optimum composition and structure and further alloy modifications aiming at improved high temperature corrosion resistance would deteriorate the mechanical and welding properties, the focus is now on the development of advanced coatings on conventional materials. These are usually Al- and/or Cr-rich intermetallic coatings applied either as overlay or as diffusion coatings. An example of the latter is shown as a two-step two-phase pack cementation coating in Fig. 4.2 and recent developments include multi-element co-diffusion coatings with up to four elements with synergistic effects with regard to protection. Such coatings offer sufficient potential for protection in highly aggressive C-, Cl-, S- and/or V-containing high temperature environments /28/.
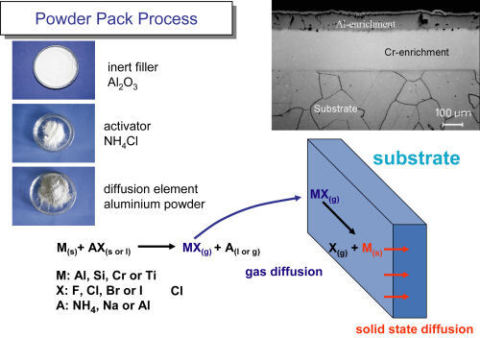
Fig. 4.2: Two-step diffusion coating prepared by the powder pack process
Even metal dusting is still a research area of significant interest, Fig. 4.3, where again the development of coatings for protection and the suppression of coke deposition have become the major focus.
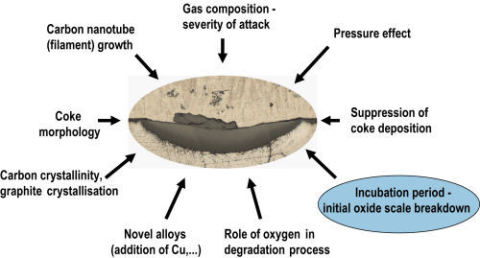
Fig. 4.3: Current trends in metal dusting research
Another issue where oxidation determines life-time is ceramic thermal barrier coatings which spall once the thermally grown oxide (TGO) between ceramic top coat and intermetallic bond coat has reached a critical state of ageing. Large research efforts are, therefore, undertaken by the jet engine industries and the manufacturers of land-based gas turbines to develop life-time models based on TGO parameters /29/. Last but not least new material classes have been developed whose oxidation/high temperature corrosion behaviour is only little known and which require new ways of protection. As an example a new class of high temperature light-weight alloys based on the stoichiometric compounds TiAl and Ti3Al can be mentioned which show an oxidation behaviour which is far away from what would be expected from the traditional understanding /30/. Even an amount of about 50% Al is not sufficient to establish a pure alumina scale in air at high temperatures. Rather a mixed non-protective fast-growing TiO2/Al2O3 scale is formed which limits the use of these materials from an oxidation point of view to about 750°C. However, a surprising effect - the so-called halogen effect - can change the oxidation mechanism in a way that only Al2O3 is formed on the surface even up to temperatures of 1050°C, thus extending the use of this group of materials dramatically, see Fig. 4.4, comparing an implanted with halogen and un-implanted surface, i.e. original state.
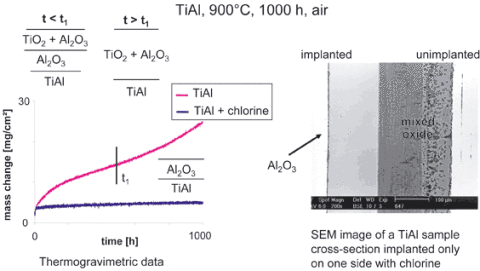
Fig. 4.4: The halogen effect on the oxidation resistance of TiAl alloys
The implantation or addition of a small dose of halogens affects the oxidation mechanism in a meanwhile understood way /31/ so that the formation of non-protective, fast-growing TiO2 is suppressed, while the formation of Al2O3 is favoured.
5. Outlook
It would be presumptuous to claim to be able to provide a comprehensive outlook on the future development of high temperature corrosion research. Therefore it is not intended to make such an attempt here. However, a good impression of the present hot topics can be obtained from the programmes of the biannual Gordon Research Conference on High Temperature Corrosion, for instance the one that took place on 24-29 July 2005 in New London, New Hampshire, which was chaired by Brian Gleeson. The programme is listed in Table 5.1 and shows that it is also the small increments on the way to new knowledge which characterize the activities of the community.
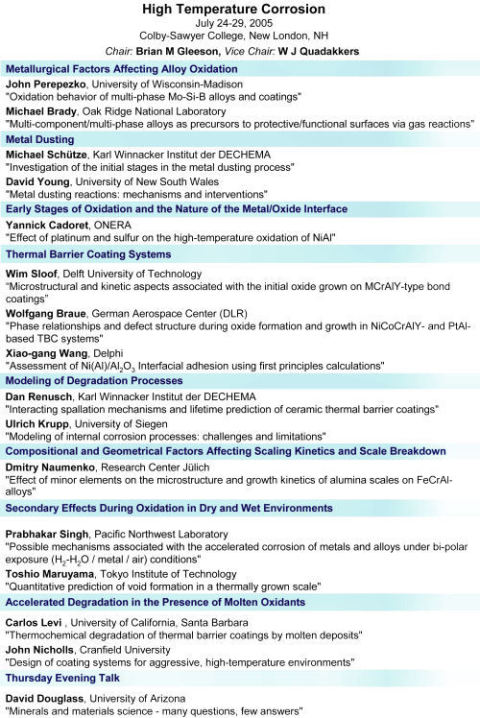
Table 5.1: Programme of the Gordon Research Conference on High Temperature Corrosion in 2005
One need not be a prophet to say that much of the development mentioned in the last paragraph has not yet reached perfection, a situation that will keep scientists and technicians busy for a while. It can, however, be suspected that high temperature corrosion research will also be used more and more to explore new ways of manufacturing multi-functional surfaces. At least at present such development has started at several laboratories.
Literature
/1/ Timeline of Corrosion History, http://www.corrosion-doctors.org/Corrosion-History/Timeline.htm
/2/ H.E. Evans, University of Birmingham, private communication
/3/ http://lexikon.freenet.de
/4/ EFC Workshop "Metal Dusting, Carburisation and Nitridation", Frankfurt/Main 30/31 January 2003, papers published in Materials and
Corrosion 54 (2003) 735-901 and as EFC vol. 41/2006 (eds. M. Schütze and H.J. Grabke)
/5/ J. Pattinson, On Carbon and Other Deposits from the Gases of Blast Furnaces in Cleveland, Journal of the Iron and Steel Institute
1 (1876) 885
/6/ K. Oberdorffer (ed.), Ludwigshafener Chemiker, Econ Verlag, Düsseldorf 1958
/7/ I. Langmuir, Chemical Reactions at Very Low Pressures, J. American Chemical Society 35 (1913) 106
/8/ G. Tammann, Die Anlauffarben von Metallen, J. Inorganic and General Chemistry 111 (1920) 78
/9/ N.B. Pilling and R.E. Bedworth, The Oxidation of Metals at High Temperatures, J. Institute of Metals 29 (1923) 529
/10/ P. Kofstad, High Temperature Corrosion, Elsevier Applied Science, London 1988
/11/ H.L. Bernstein, A Model for the Oxide Growth Stress and Its Effect on the Creep of Metals, Metallurgical Transactions A18 (1987) 975
/12/ M. Schütze, Protective Oxide Scales and Their Breakdown, Wiley, Chichester 1997
/13/ J.S. Dunn, The High Temperature Oxidation of Metals, Proc. Royal Society A111 (1926) 203
/14/ J.S. Dunn, The Low Temperature Oxidation of Copper, Proc. Royal Society A111 (1926) 210
/15/ Y. Utida and M. Saito, The Oxidation of Metals and Alloys at High Temperatures, Scientific Reports of Tohuku Imperial University ,
13 (1924/25) 391
/16/ L.B. Pfeil, The Oxidation of Iron and Steel at High Temperatures, J. Iron and Steel Institute 119 (1929) 501
/17/ L.B. Pfeil, Improvements in Heat Resistant Alloys, US Patent No. 459848 (1935)
/18/ C. Wagner, Beitrag zur Theorie des Anlaufvorgangs, Z. Physikalische Chemie 21 (1933) 25
/19/ C. Wagner, Theoretical Analysis of the Diffusion Processes Determining the Oxidation Rate of Alloys, J. Electrochemical Society
99 (1952) 369
/20/ C. Wagner, Reaktionstypen bei der Oxydation von Legierungen, Z. Elektrochemie 63 (1959) 772
/21/ H.W. Grünling, B. Ilschner, S. Leistikow, A. Rahmel and M. Schmidt, Interaction Between Creep Deformation and Hot Gas Corrosion in
"Behaviour of High Temperature Alloys in Aggressive Environments", eds. I. Kirman et al., The Metals Society, London 1979, pp. 869 ff
/22/ D.P. Whittle. J. Stringer, Improvements in High Temperature Oxidation Resistance by Additions of Reactive Elements or Oxide
Dispersions, Philosophical Transactions of the Royal Society of London A295 (1980) 309
/23/ Guidelines for Methods of Testing and Research in High Temperature Corrosion (EFC 1), eds. H.J. Grabke and D.B. Meadowcroft
back to previous page