Current Activities
Business Meeting
Next Business Meeting at the upcoming EUROCORR
Get involved!
If you wish get involved with EFC and the activities of the Working Party please click here to register!
Mission / Vision
The Working Party 13 symposium shall be a meeting place for O&G operators, industry and research institutes to share and exchange, technical developments, safety issues and test results. Aiming at improving technology, sustainability and safety for the Oil & Gas industry.
The Working Party 13 Business Meeting is meant to informally share the latest on material developments. Typically highlights on what is new, the status of ongoing research, the latest HSSE concerns and burning issues that affect our industry. Notes will not be made and slides will not be shared.
We develop guidelines and documents for new topics related to corrosion in oil and gas production.
- Sour environments
- Material selection
- Prediction, mitigation and monitoring solutions for all weight loss corrosion modes in oil and gas environments (CO2 corrosion, H2S + CO2 corrosion, MIC, erosion- corrosion, …)
Awards
Young Author's Prize
Each year since 2003 ANTIKOR, the International Scientific and Educational Corrosion Centre in Moscow, which is represented by Dr. Alexander Muradov, has kindly sponsored a prize for the best oral presentation by a young author under the age of 35 in the Oil and Gas session at EUROCORR.
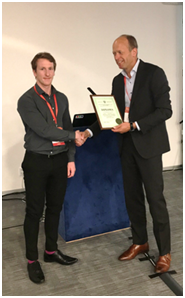
2017
The 2017 prize was awarded to James Hesketh of the National Physics Laboratory (NPL) for his presentation "The role of H2S in pitting of stainless steel in sour oil & gas applications", for which he received the maximum score in all four categories. In addition, James had an excellent contribution in the Oil & Gas Business Meeting on "Factors that can lead to discrepancies between constant load and constant displacement SCC tests".
Best congratulations from WP 13!
2016: Fiona Ruel
Aperam Stainless Europe
"Effect of the substitution of Ni by N and Mn in lean duplex stainless steels on stress corrosion cracking assisted by H2S".
2015: M. Monnot
Ugitach SA
"SSC study of a super martensitic stainless steel: role of H2S on metallic sulfur formation and hydrogen embrittlement".
2014: Ehsan Fallahmohammadi
Politecnico di Milano
"Effect of plastic deformation on hydrogen permeation of API 5L X65 steel Pipeline"
2013: Gaurav Joshi
University of Manchester, United Kingdom
" Elucidating sweet corrosion scale"
2011: Michaela Hoerstemeir
Salzgitter Mannesmann Forschung, Germany
"Sulfide Stress Cracking Resistance of High strength Low Alloy Steels for High H2S pressure Wells"
2010: Anna Smirnova
University of Science and Technology, Norway
"Effect of tensile stress on hydrogen diffusion in 13% Cr supermartensitic stainless steel"
2009: Christelle Augustin
Vallourec, France
"A better Control of pH Drift when Testing SSC in Fit For Purpose Conditions"
2008: Magnus H. Larson
Nexans, Norway
"Crevice corrosion of super dublex steel tubes in sub-sea umbilicals"
2007: Véronique Smanio-Renaud
"Use of Acoustic Emission for the Study of Hydrogen Induced Cracking in Steels"
2006: Kenji Kobayashi
"Effect of testing temperature on hydrogen absorption and SSC behaviour of high strength alloy steel"
2005: Delphine Zuili
"A case history of environmental cracking in sour service - Sulphide-Chloride ions stress corro-sion cracking on 316L stainless steel"
2004: Tomohiko Omura
"125 ksi grade high strength low alloy steel OCTG for mildly sour environments"
2003: Sebastien Duval
"Hydrogen permeation in iron membranes under various charging conditions including wet H2S"
Publications
- EFC Publication No 17:
"Corrosion Resistant Alloys for Oil and Gas Production: Guidance on General Requirements and Test Methods for H2S Service", 2nd edition - EFC Publication No 16:
"Guidelines on Materials Requirements for Carbon and Low Alloy Steels for H2S-containing environments in Oil and Gas Production", 2nd edition.
- EFC Publication No 23:
"CO2 Corrosion Control in Oil and Gas Production - Design Considerations"
- EFC Publication No 32:
"Working Party Report on the Life Cycle Costing of Corrosion in the Oil and Gas Industry: a Guideline" - EFC Publication No 39:
"The Use of Corrosion Inhibitors in Oil and Gas Production" - EFC Publication No 55:
"Corrosion under insulation (CUI) guidelines" - EFC Publication No 64:
"Recommended practice for corrosion management of pipelines in oil and gas production and transportation"
Previous Activities
Minutes from WP meetings
- Minutes of the WP13 meeting on Paris in September 2024
- Minutes of the WP13 meeting in Seville in September 2019
- Minutes of the WP13 meeting in Krakow on 10 September 2018
- Minutes of the WP13 meeting in Graz on 8 September 2015
- Minutes of the WP13 meeting in Pisa on 10 September 2014
- Minutes of the WP13 meeting in Estoril on 4 September 2013
Appendices to the minutes - Minutes of the WP13 meeting in Istanbul on 13 September 2012
- Minutes of the WP13 meeting in Stockholm on 9 September 2011
- Minutes of the WP 13 meeting in Moscow on 13 September 2010 + given presentations
- Minutes of the WP 13 meeting in Nice on 10 September 2009
- Minutes of the WP 13 meeting in Edinburgh on 10 September 2008
Appendix A , Appendix B , Appendix C , Appendix D , Appendix E , Appendix F , Appendix G , Appendix H , Appendix I , Appendix J , Appendix K , Appendix L - Minutes of the WP 13 meeting in Freiburg on 13 September 2007
Appendix A , Appendix B , Appendix C , Appendix D , Appendix E , Appendix F - Minutes of the WP 13 meeting in Maastricht on 25 September 2006
- Minutes of the WP 13 meeting in Lisbon on 7 September 2005
- Minutes of the WP13 meeting in Nice on 15 September 2004
- Minutes of the WP13 meeting in Budapest on 2 October 2003
In Memoriam - Stefan Winnik
Joint NACE/EFC Workshop, Freiburg, 10 September 2007
Operator's Views: Current Status and needs for Future Research related to
Corrosion in Oil and Gas Production"
A joint NACE/EFC Workshop was organised during the EUROCORR 2007 conference.
Specially invited speakers from oil and gas companies presented papers on 8 different topics related to corrosion in the oil and gas industry. The presentations gave Operators Views on the "Current Status and Need for Future Research Related to Corrosion in Oil and Gas Production".
The following speakers contributed to the workshop:
- Stress corrosion cracking of stainless steels in chorides environments, T. Cassagne, Total S.A. Pau, France
- H2S cracking, J. Martin, BP Exploration Operating Co. Ltd., London, UK (see Attachment 2)
- Corrosion fatigue in SCRs and armours in flexibles, R. Thompson, Chevron Corporation, Houston, Texas, USA (see Attachment 3)
- Materials in wells, P. Nice, Statoil A.S.A. Stavanger, Norway (see Attachment 4)
- CO2 corrosion and inhibition, M. Achour, ConocoPhillips, Bartlesville, Oklahoma, USA (see Attachment 5)
- Corrosion in water injection, T. Andersen, Norsk Hydro A.S.A., Porsgrunn, Norway (see Attachment 6)
- Cathotic protection and coatings, S Kapusta, Shell Global Solutions, Rijswijk, The Netherlands (see Attachment 7)
- Corrosion in seawater, S. Olsen, Statoil Research Centre, Trondheim, Norway (see Attachment 8)